At the Consumer Electronics Show (CES), earlier this year, Plessey unveiled augmented reality (AR) and virtual reality (VR) glasses using microLEDs and which ditched OLEDs completely.
According to Plessey, these microLEDs were able to offer 10 times the resolution, 100 times the contrast ratio, and up to 1,000 times the luminance of traditional OLEDs, all of which was achieved by the light being generated directly by the pixels themselves. They’re able to turn off entirely to create a so-called “perfect” black, which means that the overall image has a far greater sense of vibrancy and depth while power consumption is reduced.
Plessey also used CES to show off a 0.7 inch 1080p microLED comprising of separate red, green and blue panels, and an addressable blue 0.7 inch microLED display running 1080p video.
The company has developed a scalable and repeatable GaN-on-Silicon monolithic process that is able, according to the company, to guarantee uniformly high quality and exceptional performance and has eliminated the problems associated with more traditional pick-and-place manufacturing techniques.
“We see our microLEDs going into the three main product areas,” explains Clive Beech. “The first is backlight systems in large screens. In combination with quantum dot films we are able to produce very high quality colour images but also the smart backlights are zoned so that they effectively carry a low-resolution monochrome image when the film screen carries the higher resolution image. So, it’s a low power, high brightness television system.
“The other one is where people are making screens by placing red, green, and blue LEDs. We can actually make a tricolour small colour pixel for that sort of application of mass transfer.”
The third area, as demonstrated at CES, is with wearable AR/VR systems.
“At the moment there are really only three solutions for this type of application,” Beech suggests. “There are two types of reflective display illuminated by a light source - Liquid Crystal on Silicon (LCOS) is one, and DMD, or Digital Multi-Mirror displays, another. Both are illuminated and the light goes directly into the projection lens and then into the glasses worn by the viewer.
“The third type of system is an OLED display, which can be designed to be very small.”
According to Beech, “The first two, the reflective designs, are not particularly suitable. When it comes to AR, you only light up about 20% of the pixels at any one time and reflective displays have to be illuminated completely because the system doesn’t know which pixels need to be on. It means that you have to power up the whole of the display, which will require a substantial battery pack to operate.
“The OLED option is a much better option as you only light up the pixels that you’re going to view. The problem with OLED, however, is that they’re not particularly bright and they don’t couple well into the optics. So, the display is very much like a normal television display and it’s visible over a wide range of angles. In an AR/VR headset we need the light to go into the projection lens, so most of the light produced by the OLED display is wasted.”
Beech argues that microLEDs overcome these problems.
“They make AR systems more achievable as you’re only lighting the pixels that you use and they’re considerably brighter than an OLED – up to 250 times – and that makes it more than capable of being visible against an unattenuated outside world.”
Because of that capability Plessey finds that many large tech companies looking to enter the AR market are keen to talk to them.
“Reflective displays don’t work for them because of their high-power consumption, and OLED doesn’t work because it’s not bright enough. So, we’re working to develop a full emissive display for augmented reality systems, in particular, and probably VR as well. The problem with VR systems is that they get very hot.”
They get hot because VR systems, unlike AR, tend to be enclosed environments, as Beech explains.
“They’re very unpleasant to use, they get very hot as they rely on DMD or LCOS displays. OLED is ok, as it’s not competing against the outside world, but they are not particularly efficient. If you want brightness in your image then those devices will tend to get very hot indeed.”
Replacing DMD and LCOS
microLEDs are a suitable replacement for DMD and LCOS, particularly in AR, according to Beech.
“We’re working with our own technology which is gallium nitride on silicon (GaN-on-Si). Now one thing about that is it makes these LEDs produce blue light. Blue light is just one of the three colours that you need. So, we are working with Nanoco Technologies to add red and green light.”
Nanoco is a manufacturer of quantum dots and semiconductor nanoparticles for use in displays and lighting and the two companies are looking to shrink the pixel size of monolithic microLED displays by using Nanoco’s technology.
Plessey wants to integrate the quantum dots into selected regions of blue LED wafers in order to add red and green light.
“This technique means we can shrink the pixel size from today’s 30µm to just 4µm, a reduction of 87%. The process will enable the production of smaller, higher-resolution, microLED displays in applications such as AR/VR devices and wearables, while enhancing both colour rendition and energy efficiency,” according to Beech.
“Quantum dots produce very pure reds and greens, so you get a good colour gamut.”
The process of transferring this technology to the micro display, which is what is needed for augmented reality, is not without its problems.
“The flux of photons going in is very high, much higher than you would have on a television screen. So, these quantum dots need to be engineered to take very high photon flux without being saturated or destroyed by that process.”
The manufacturing process, that’s being developed with Nanoco, is complex but market leading.
“We’ve got the performance up to a very high level and I believe it’s a technology whose time has come. ” Clive Beech |
“Our displays are arrays of microLED dots but as an array, it’s not controllable, so it has to be bonded to a CMOS backplane. The backplane controls all the LEDs to give us, effectively, a monochrome display. What we then have to do is to take those monochrome pixels, around a third, and colorize them to red with quantum dots, and another third to green.
“In order to do that, we’ve got to be able to print quantum dot material at the scale of just a few microns in size.
“A pixel is eight microns by eight microns, and that pixel has to be sub-divided down into red, green and blue. So, the red pixel will be two by eight, and the green will be two by eight, and the blue, at the side of it, will be two by eight. There’ll be a small gap between each. So, the two big challenges are that the quantum dots have to survive the high flux density and the high temperatures associated with these displays.
“We’ve then got to be able to print them, but on a very small scale. We are looking at something of the order of two or three microns in size. They’ve got to survive the high flux density. They’ve got to survive the local high temperature. And they’ve got to
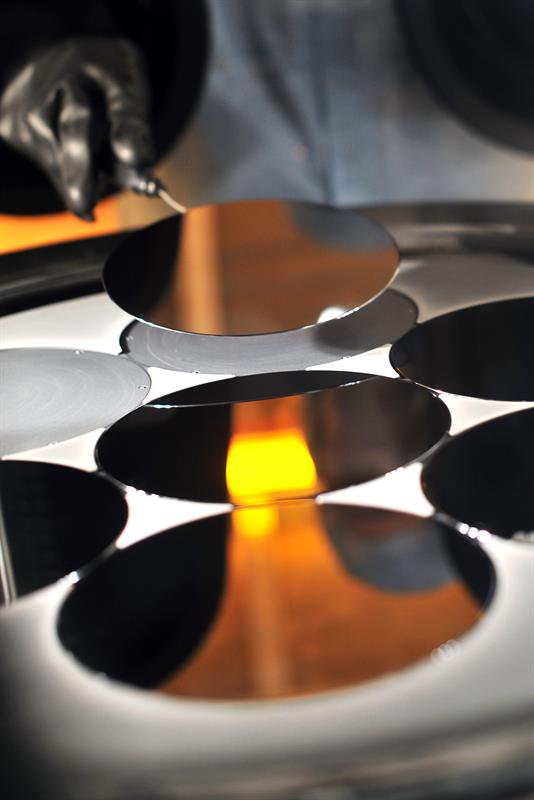
be protected from the outside world. Those are not insignificant problems to be overcome.”
Plessey has a number of microLED contracts in place with leading tech companies, according to Beech.
“They all want different sizes, different size pixels, but most of those will have prototypes in their hands in Q4 this year and pre-production samples will be available around that sort of time; our aim is to have product in the market next year.”
microLED adoption is expected to accelerate post 2020, yet in the mobile space its brightness is an issue, and the cost of microLED displays remains prohibitive.
“OLED displays work well enough. At present microLEDs would be very expensive to use - so for phone screens it’s not really an option,” said Beech.
“We’ve got the performance up to a very high level and I believe it’s a technology whose time has come. We are hitting a point where the adoption of microLEDs is certainly accelerating, but the challenge remains manufacturing at scale."
Plessey’s displays are arrays of microLEDs bonded to a CMOS backplane |