New process could prevent cold cracking in high strength steel
1 min read
Scientists at the Fraunhofer Institute for Mechanics of Materials IWM have developed a new process for making cold cracking in high strength steel more predictable.
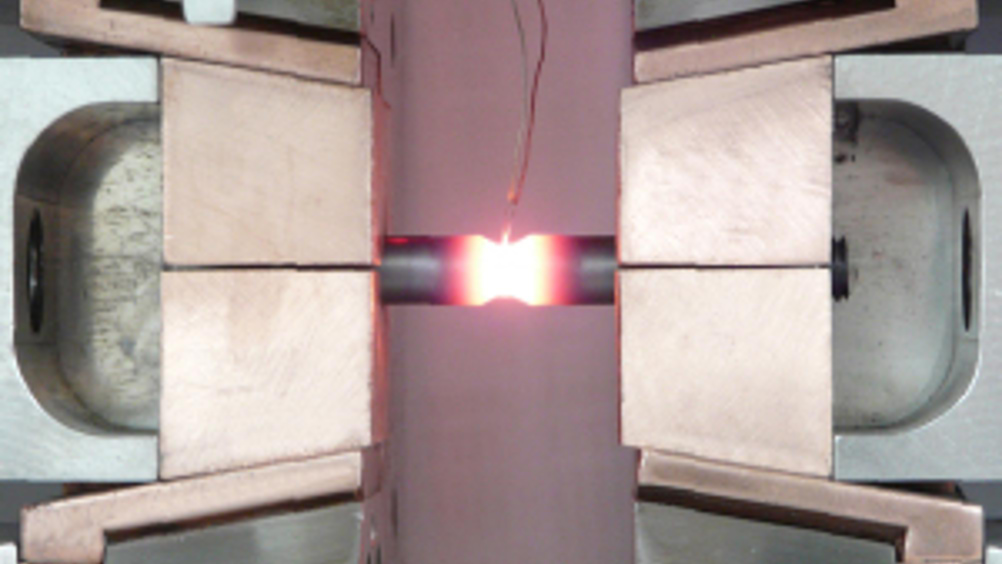
Cold cracking currently presents major quality assurance challenges for the automotive and machine building industries, but the scientists say their new method could lower both development time and costs.
"We are able to compute the probability of cold cracking as early as the design stage of a component, and immediately run through corrective measures as well," explained Frank Schweizer at the IWM.
The new approach uses a test which takes into account typical influencing factors such as hydrogen content, residual stresses and material structures as well as temperature gradients that emerge in the welding process. A computer simulation is fed with this information in order to analyse the threat of cold cracking in random components and geometries.
"This way, we can locate the areas on a welding seam at risk of cold cracking, for each point and at any time in the simulated welding process," added Schweizer.
The team can also get a preliminary look at the effects of any countermeasures, and make the necessary adjustments by transferring the results back into the simulation.
With this process, manufacturers could potentially be able to define non critical welding parameters and limiting conditions for their materials in advance and establish a safer and more efficient production process.