We are all very dependent on the infrastructure around us, so the sooner changes and issues can be detected, the lower the cost of remedial works. Yet, detecting the smallest changes requires technology with the ultimate accuracy that is also reliable and robust in challenging environments.
This need for structural health monitoring is helping drive demand for sophisticated MEMS technology whether for large structures such as bridges and tunnels, historic buildings, tower blocks or other civil projects such as hydroelectric dams.
There are many things that can affect these structures, causing small – almost imperceptible – changes that if not addressed can lead to damage and potentially catastrophic failure or collapse, losing the structure and threatening lives. Many of the causes can be natural: earthquakes, avalanches, snow load or simply the ground that the structure is built on shifting over time. In other cases, the cause can be man-made; poor workmanship or materials, vibration from traffic or construction work in the vicinity are just three examples.
In order to provide early warning of issues so that they can be addressed and remedied, many important structures are now implementing structural health monitoring (SHM). Through the attachment of sophisticated sensors, critical parts of the structure can be monitored, even remotely, giving structural engineers warning of even the slightest movement.
In fact, it is becoming commonplace that major infrastructure projects such as London’s Crossrail or the Blue Line extension project in Bangkok implement SHM to monitor the project and the surrounding environment and structures. Especially in modern crowded cities, infrastructure projects often involve the boring of tunnels through crowded areas – even below ground there are hazards such as existing tunnels, sewer pipes, cables and more that must be avoided. The new tunnel may well pass under rivers, highways, bridges and significant structures all of which could be affected by boring too close, or the vibration caused by the huge tunnel boring machines.
Typically, an SHM sensor consists of the sensor element itself and a mechanical arrangement such as a bar or plate that is designed to be fixed directly to the structure.
SHM will be used to monitor the new tunnel itself to ensure that it is stable, and other tunnels that are close by as well as the surface and significant structures. In the case of London’s Crossrail, the new tunnel passed within a few metres of existing subway tunnels and close to the famous Big Ben clock tower, where engineers were concerned if the structure moved by more than 30mm as a result of the works.
Challenges of accurate SHM
Given that SHM involves monitoring changes of just a few millimetres in structures that can measure hundreds of metres, often in inhospitable and remote locations, there are many challenges in developing SHM sensors.
Accuracy of the sensing element is critical to be able to measure the small changes involved, as is repeatability – if the structure is not moving, then the sensor must indicate that. Similarly, the sensing element must be stable over time and not age, otherwise a false indication of movement could be created.
As the movements and signals are small and often transmitted over relatively long distances (from the top of a tower to ground level, for example) then a good signal-to-noise ratio is needed to be able to pick out the valuable information from any noise signal that is present.
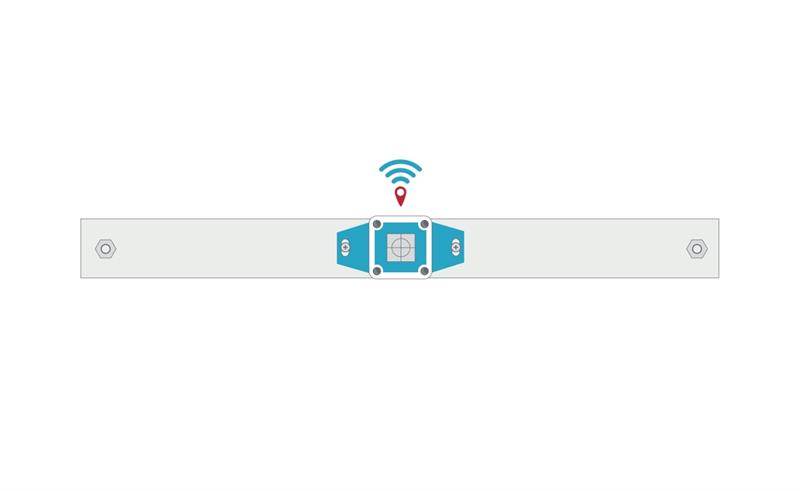
As the sensors are commonly installed in outdoor locations, they are subject to temperature fluctuation depending on the location and weather conditions which can be exacerbated by being mounted in a sealed housing.
Figure 2: Example of a tilt beam sensing device for SHM |
Reliability is another obvious requirement. While sensor failure is relatively easy to detect, the cost of replacing a failed unit can be expensive as they are often mounted in relatively inaccessible locations that require specialist access equipment, or in very remote locations.
In many of the places that SHM sensors are installed, reliable power may not be available, or wiring may not be permitted due to the historic nature of the building. As such, low power consumption is a key requirement in these applications.
At the heart of many modern SHM systems is a small accelerometer device based upon MEMS (micro electro-mechanical system) technology. In simple terms this consists of a mass that is suspended on springs that moves in response to changes in acceleration, including earth gravity acceleration as the sensor is tilted. These movements affect the capacitance values of close-coupled capacitive devices and provide an electrical output that is proportional to the acceleration experienced by the sensing element.
Murata’s SCA3300 is a 3-axis industrial accelerometer/inclinometer that is suitable for use in multiple SHM applications to monitor the angle and vibration measurement of structures. Based upon the company’s 3D-MEMS technology, the SCA3300 is designed, manufactured and tested for high stability, reliability and quality requirements. It is able to measure a wide range of accelerations between ±6g and users are able to select measurement ranges as low as ±1.5g to improve resolution. The low noise density of just 40µg/√Hz ensures that high-resolution measurements are possible.
Figure 3: Murata’s SCA3300 3-axis accelerometer is based upon proven 3D-MEMS capacitive technology |
The device shows excellent bias stability over time, ensuring good long-term monitoring of structures and readings are not materially affected by temperature fluctuations due to the ±15mg temperature offset performance. The sensing element is mechanically damped to give superior vibration robustness and the device is shock resistant, allowing use in harsh environments.
Along with the MEMS sensing element, the sealed plastic package contains a mixed signal ASIC that processes the output from the sensing element and transmits this via the integrated SPI interface.
The SCA3300 can operate in ambient temperatures from -40°C to 125°C and consumes just 1.2mA when operating allowing for battery powered operation in remote or inaccessible locations. As the device only needs to be powered on when a measurement is being taken, long lifetimes are possible with even the smallest of batteries.
Using advanced capacitive 3D-MEMS technology and similar to the SCA3300 is the SCA103T analogue high performance single-axis inclinometer. This device is commonly used in handheld levelling tools and other levelling instruments.
The SCA103T is said to be the world’s most accurate inclinometer that is in mass production and offers measurements up to 30° across a temperature range of -40°C to 125°C with a resolution of 0.0013°. In the range -40°C to 85°C, the output is only affected by temperature by 0.002°/°C. Noise densities are exceptional at just 7µg/√Hz, significantly contributing to the high levels of accuracy.
In common with the SCA3300, the SCA103T offers shock resistance and has mechanical damping to limit the frequency response to 8-28Hz, eliminating high frequency vibration.
The SCA103T has a ratiometric analogue output that delivers the very highest levels of accuracy for demanding applications.
SHM is becoming an essential part of the modern world, monitoring structures as they age or during periods of construction. With accurate and reliable SHM, structural engineers can monitor any changes and adjust maintenance schedules or design repairs as necessary, ensuring a long life and safe operation.
Author details: Antti Viitanen is Business Development Manager, MEMS sensors, Murata Elektronik GmbH |