Twenty years ago Cal-Poly’s Jordi Puig-Sauri and Bob Twiggs, then at Stanford University, came up with a plan to make it easier for their students to put satellites in orbit. Standardisation was seen as crucial in making that happen and today, hundreds of tiny low-cost satellites now orbit the planet.
Forcing every satellite into the same footprint meant it was easier to mix and match the systems from different groups in one part of the nosecone away from much more costly payloads that would share the ride.
The design for the CubeSat’s protective pod remains brutally simple and reliable: a metal jack-in-the-box.
Once in orbit and any protective shields have been blown off after payloads have been deployed, a strong spring pushes the cuboid satellites in each square tube out into space.
Puig-Suari and Twiggs decided against putting a locking mechanism on the door that covers the tube during launch for fear of one or more jamming at the crucial moment, that means the cuboid satellites inside receive a strong buffeting during launch. However, good mechanical and electrical design could handle this problem even with commercial parts. Today, a number of projects use connectors with latching mechanisms, such as Harwin’s Gecko, so that the electrical connections do not work loose during the launch.
Although the CubeSat standard made it much easier and cheaper to get projects into space, progress remained slow until 2013. Launches more than trebled to 88 with not just research institutes getting onboard but companies as well. In 2014, corporate launches overtook those of the research community and account for the majority of nanosatellites in orbit.
While the total value of the CubeSat market is growing it is dwarfed by the the wider small-satellite market. The difference is that while it may only cost $10K to put a single, basic CubeSat into low-Earth orbit, a satellite the size of an office printer – which is still considered small in satellite terms – can cost $1m to develop and launch.
Nicolas Ganry, Microchip Technology product marketing manager, says a key advantage of large constellations of nano-satellites such as CubeSats is their ability to provide real-time coverage of what is happening on Earth. They may have lower-resolution imagers than their larger colleagues but with the ability to point larger, more capable satellites to significant events. “These new constellations can complement traditional constellations,” he says.
Cooperation in action
An example of cooperation in action is a deal between Spire and ICEye to track seaborne piracy. The large Spire constellation tracks the AIS radio transponders used by ships to identify themselves. When a ship switches off its transponder, it is often a signal of illegal activity. At this point, the Spire network identifies ICEye, which uses the radar in its satellites to track the targets that have gone dark.
CubeSats tend to be short-lived. More than 300 so far have been inserted into orbits with a perigee of less 400km, just below that of the International Space Station. Just over a hundred are still in orbit: atmospheric resistance has dragged the others to a fiery demise. Operators such as Spire see this natural deorbiting as planned obsolescence. It allows regular upgrades in performance as new versions replace those that have burned up.
Although many CubeSats do not last for long, more than 300 are now in higher orbits and with expected lifetimes of 10 years or more. Two set off a year ago into deep space on a mission to Mars. Others are planned for orbits that will take them close to the sun. These longer missions place much greater emphasis on the reliability of the electronics, which have to operate under extremes of temperature and suffer bombardment of cosmic rays.
Strikes from ionising radiation generally results in the release of a cloud of charge particles into the silicon substrate underneath transistors and memory cells. Most of the time, these collect in registers and memory cells, possibly flipping their state in single-event upsets.
A more serious problem is permanent latch-up caused by the charges interacting with parasitic bipolar transistors that form in the junctions between doped semiconductor wells. If it occurs,
the device will fail and possibly the entire satellite if the designers could not afford to include a backup.
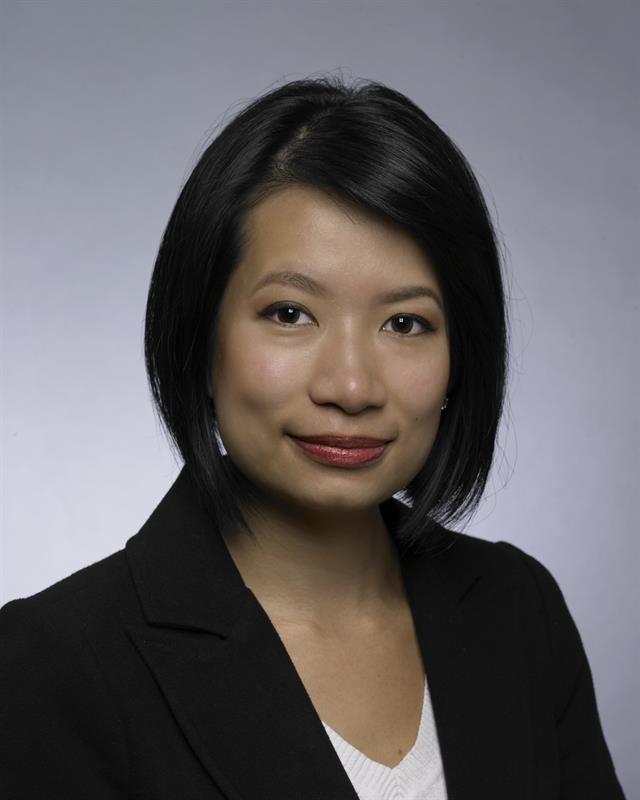
Components designed for use in space to handle radiation and temperature extremes are generally tested and supplied under programmes based on the Qualified Manufacturers List (QML) regime operated by the US military. This defines tests down to wafer-lot level to check parts for resilience and
reliability. But if they come to demand full military-grade parts, many small-satellite designs become uneconomic.
CubeSat and nano-satellite designers have explored a number of ways to buy and, if necessary, tweak commercial-grade parts to work reliably in space.
“Small-satellite designers tended to underestimate the problems radiation cause for satellites with short operational lifetimes.” Minh Nguyen |
Minh Nguyen, senior manager of product marketing at Microchip Technology says small-satellite designers have tended to underestimate the problems radiation cause for satellites with a short operational lifetime and so make do with automotive or industrial-grade parts that do not go through extensive radiation testing. In practice, radiation can be problematic even for short-lived satellite. A growing number of design teams are recognising this, she notes. At the time, commercial-grade parts are being hardened up for space use.
Bridging the gap
To try to bridge the gap between military-grade and commercial parts, Microchip has a Sub-QML programme for FPGAs and other parts: “These devices have proven radiation and reliability so we don’t have to do additional reliability testing for every wafer lot. That way we can cut down the purchase cost to make it attractive for these missions,” Nguyen says.
One strategy some designers employ is to use a comparatively rad-hard system controller, perhaps based on an antifuse-based FPGA, that monitors a cluster of less-resilient processors and devices and resets them if a problem emerges, assuming one or more does not suffer a latchup failure. Nguyen says the antifuse technology continues to provide more resistance to radiation than flash-based programmable logic, though flash offers greater protection against single-event upsets than SRAM .
Ferroelectric (FRAM) and magnetic memories also perform well in space. “Total ionising dose levels of more than 1Mrad have been measured repeatedly for FRAM memory cells,” says Helmut Puchner, Cypress fellow and vice president. In practice, the radiation susceptibility of an FRAM is largely due to CMOS registers in the periphery and control circuits. A number of LEO-bound projects have used automotive-grade FRAMs, he adds, but the company is currently qualifying a hardened 2Mbit FRAM for higher orbits.
Vorago Technologies has pioneered the use of an implantation process to improve the latchup immunity of commercial foundry processes. This puts high-conductivity guard rings underneath active transistors to prevent the potentially destructive parasitic devices from activating. The company has licensed the HardSIL process to other chipmakers to modify their own products as well as using it to provide hardened processors based on the Arm architecture.
Many small satellites currently use 8bit or 16bit processor architectures but interest is growing in more capable 32bit parts. Microchip has plans to harden some of its own commercial-grade Arm-architecture and 16bit processors for use in future projects. Similarly, Cypress is exploring the development of a radiation-hardened Arm-based PSoC with embedded flash.
As their lifetimes increase, the need to pack more valuable instruments into each launch goes up. These systems also have a greater need for propulsion to control their orbits, which restricts internal space even more. Ganry says size constraints is likely to lead to greater use of distributed design techniques with more intelligence placed close to the sensors peripherals instead of concentrating processing in a central control board.
A graph of launches since 1998 compiled by nanosats |
Agencies such as NASA are looking at using multichip modules to save space and have awarded contracts to test ideas. Under one of these contracts, Vorago is beginning to assemble a module test vehicle based on a ceramic substrate that the company expects to be ready to fly by the end of the year. The result will be that even more compact forms of low-cost satellites will soon be on and flying over the horizon.